
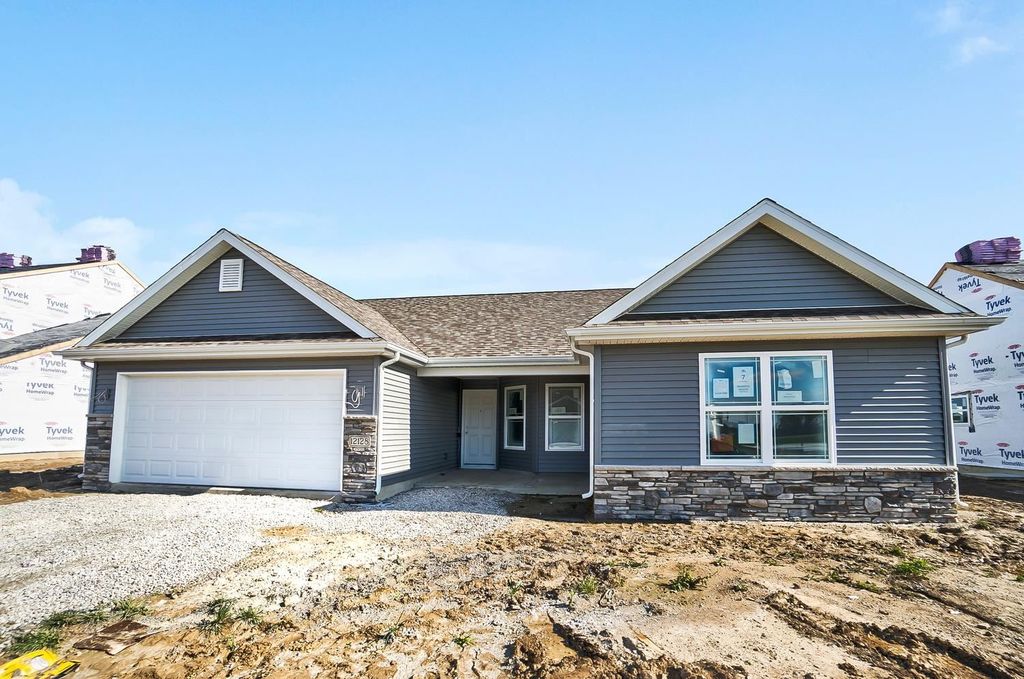
Housing a cylindrical gear motor, the stationary drive unit causes the pan to stroke forward slowly and then back quickly. Each FastBack module consists of a stationary drive and a stainless-steel pan measuring 2' across and as much as 25' in length. Supplied by Heat and Control, these conveyors transport product to whichever bagging machines are appropriate. Product flow into the packaging room is also improved through the use of FastBack(TM) horizontal-motion conveyors. That company provided the plant layout shown on page 38. From east to west, it will be a smooth flow of packaging materials to packaging machines to palletizing to the finished goods warehouse."Īssisting in designing this smooth flow, adds Anderson, was contractor/engineer Shambaugh & Son (Fort Wayne, IN). "Once we have all the packaging equipment in one large room," says Anderson, "we'll add another 30ꯠ square feet with some dock doors, and then all packaging materials will enter the plant through those dock doors. In the new plant, only five of the 23 scale/bagger combinations are still located outside of the new packaging room, and they'll join their mates as soon as some older ovens are replaced by new ones in the new oven area. Pretzel packaging, for example, was in the center of the plant, with no room around the existing machines to allow for expansion. In the pre-fire plant, packaging was done in three different plant locations. Bag weights range from 3/4-oz to 3 lb.Ĭhief among the benefits of the new layout is the consolidation of all packaging equipment in one room. Each bagger is equipped with an AK-15 hot stamp imprinter from Norwood (Downers Grove, IL). The Ishida scales are from Heat and Control (Hayward, CA), the Ultima baggers from Hayssen (Duncan, SC). Included in that "everything" are 23 combination scales mounted over 23 vertical form/fill/seal baggers. And by August, "Everything was up and running," says Anderson. By July, just seven months after the fire, both extruded snack products and pretzels were in production in a newly built facility on the same site.
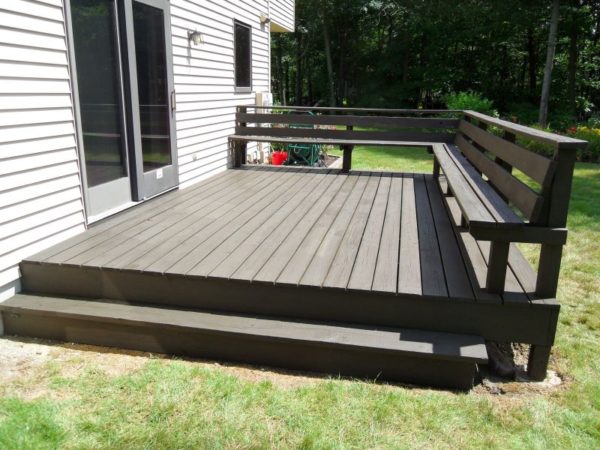
The privately held snack maker didn't waste any time, either. "It enabled us to look back at what we'd done piecemeal over nearly 20 years and redo it all with what we know today," says senior vice president and general manager Tom Anderson. of Bluffton, IN, went up in flames on Christmas Eve, 1997, the disaster came with a silver lining. No company wants to see its main manufacturing plant leveled by a devastating fire.
